House Grants
Victoria residents who own Heritage Designated homes can apply for financial assistance to help with the upkeep.
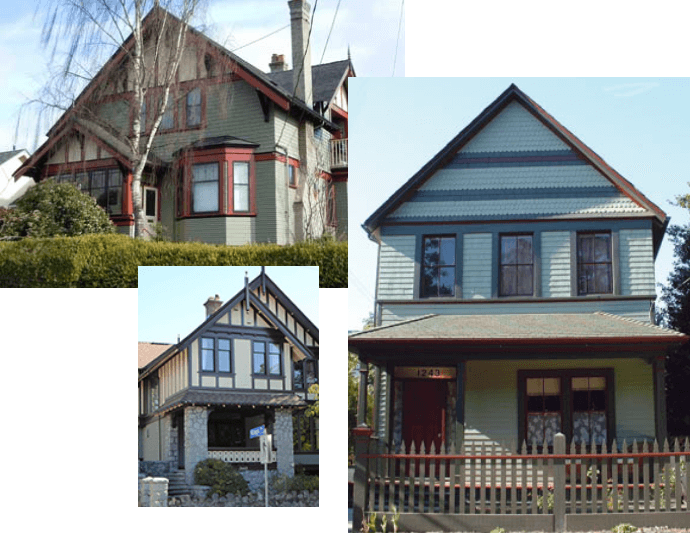
Application Guidelines
The House Grants Program of the Victoria Heritage Foundation (VHF) promotes the retention and preservation of Victoria’s irreplaceable historic housing stock by assisting owners of Heritage Designated houses with the costs of rehabilitation and maintenance.
Each year VHF receives funds from the City of Victoria and allocates them to homeowner applicants. Owners may submit one application per year per property, but an application may contain more than one project. The House Grants Program covers a portion of project costs, subject to VHF priorities and the availability of funds. If a grant is approved, the work should be completed within the year.
VHF has set clear guidelines and priorities for approving applications. The relevant forms, requirements, and guidelines can be accessed through the links below.
Due to the high volume and value of grant applications, all submissions must be made by March 31st each year. This ensures that the funding percentage for the year’s grants can be determined in April. If projects are cancelled, it may free up additional grant money, allowing for a second intake of applications in September.
Funding amounts vary each year based on the number of applications received and the amount of grant funding received from the City of Victoria. The grant may cover up to 50% of the project’s cost.
To view a complete list of the previous year’s grants, see the VHF Annual Report
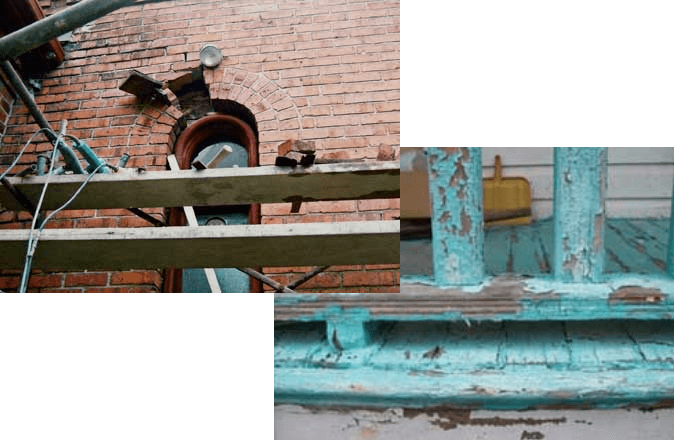

Ensure that your project and quotes conform to the VHF Rehabilitation Requirements. Adherance to the Rehabilitation Requirements is mandatory. It is the homeowner’s responsibility to ensure that work is done per the requirements. Failure to comply with these requirements will likely affect payment of your grant in full or part. To ensure full compliance, please provide prospective contractors with a copy of the applicable requirements for the project and ask them to specify these requirements in their quotes. The contractor’s on-site representative should also be provided with a copy before work commences.
Use contractors who have experience working on heritage houses and with positive references you can personally verify.
● An overall rehabilitation plan is highly recommended.
● Ongoing maintenance will minimize the need for extensive repairs.
● Repairs to the basic structure, foundations and roofs should be done first.
● Repair of historic materials is preferable to replacement with new work.
● If original detail is missing or replacement is necessary, new work should accurately match the original forms, materials and detailing, based on sufficient physical or documented evidence.
● Use products with proven performance records.
● All surface cleaning should be undertaken with the gentlest method possible.
● Use contractors who have experience working on heritage houses and positive references you can personally verify. Although the owner’s labour is not eligible for grant, materials are eligible.
● When obtaining quotes for a project, make sure you have considered all aspects of the job. Additional costs may not be funded.
While every effort is made by the Victoria Heritage Foundation to provide correct information and guidance to homeowners in making applications, neither VHF nor its members or staff individually guarantees the information given.
Seismic Upgrading
Victoria is in a high-risk earthquake zone. VHF urges homeowners to consider seismic upgrading both for personal safety and protection of their investment in Victoria’s irreplaceable historic housing stock. VHF strongly recommends that homeowners purchase Earthquake Insurance.
Although the 2012 Building Code includes prescriptive seismic guidelines for new construction, these are most likely not directly applicable to heritage-type buildings.
- Seismic upgrading for foundations of heritage-type construction, masonry chimneys and roof structures must be designed by a Professional Structural Engineer in order to be eligible for a grant.
- Where seismic upgrading is planned, homeowners can expedite the process by obtaining the required engineering design along with the contractors’ quotes, and submit these with the grant application. The cost of the engineering documentation is eligible as an additional grant to that allotted to the construction (see Special Grants in Application Guidelines & Conditions).
Download or print Foundations & Seismic Upgrade Requirements
Foundations
VHF funds foundation repair as well as some new foundations.
- Foundations as part of major basement renovations may not be funded and will be reviewed on a case-by-case basis after all city permits are approved.
- Any foundation that raises the house will be considered on a case-by-case basis.
- Reconstruction of foundation skirting should replicate the original, including water table elements.
Download or print Foundations & Seismic Upgrade Requirements
Chimneys & Masony Work
VHF funds only exterior brick and masonry work. Make sure your contractor is familiar with historic masonry work.
- When rebuilding a chimney, reuse original bricks or stone wherever possible.
- Replacement bricks or stone, if required, should closely match the original in profile, colour, texture and size.
- Do not use soot-stained bricks on exterior.
- Cleaning or paint removal should be undertaken with the gentlest method possible.
- Media (e.g. sand) blasting and power washing are not acceptable.
- When repointing mortar joints, power tools are not recommended for use on vertical joints and considerable care is required for their use on horizontal joints.
- Strength, composition, colour, texture and profile of mortar joints or pointing should closely match original.
- Mortar should be weaker than the bricks. Historic brick construction used soft lime mortars with a minimum of Portland cement.
- Counter-flashing on brick chimney sides should include stepped (rather than continuous) and inserted into horizontal mortar joints and re-mortared. If previous counter-flashing was set into a diagonal groove cut into bricks, this must be repaired with colour-matched mortar.
- Profile and material of chimney cap and chimney pots should closely match original; try to find old photographs. Beware of reproducing a chimney that has been rebuilt incorrectly in previous years.
- If installing flue liners (not funded by VHF), use minimum projection above chimney.
Windows & Doors
It is preferable to repair rather than replace original wood sash windows. The key to window longevity is the quality of the original material and construction techniques, combined with regular maintenance. These general guidelines for historic windows also apply to the repair, restoration and replication of historic doors.
- VHF funds repair and restoration of historic windows.
- VHF funds replication of historic windows where the original windows are missing or beyond repair.
- VHF does not fund double-glazed or thermal units.
- Replacement windows must replicate the original windows in material, overall frame size, sash profile and size, muntin profile and size, glass colour and reflective qualities.
- Replace windows with historically appropriate or vintage glass.
- Wood muntin bars separate pieces of glass. They are not placed over one large pane of glass.
- Loose and deteriorated window putty must be removed and replaced with linseed oil glazing putty. Linseed oil putty requires 2-4 weeks drying time before painting with oil or alkyd primer.
- It is recommended that visible hardware such as hinges, door handles, locks and escutcheons be appropriate to the period and style of the house.
- Modern weather stripping, door sweeps and deadbolts should be as unobtrusive as possible when viewed from the exterior.
- To be eligible for VHF funding, weatherstripping should be durable and not visibly alter the profile of the window/door or jamb. Some examples include:
– Silicone tube seal set in a groove
– Spring bronze
– Interlocking metal
Recommended: Consider using historic “wavy” glass appropriate to the period of the house be used rather than modern float glass.
Storm Windows
Storm windows can increase the life of historic windows by providing protection from the elements as well as heat and sound insulation. To obtain the highest efficiency from a wood storm, the existing window should be well maintained, operable, tight fitting and retrofitted with weatherstripping.
- VHF funds fixed and opening traditionally-constructed (jointed with through-mortise and tenon joinery) wood storm windows.
- Storms must be attached with non-invasive hardware such as storm hangers.
- It is recommended that all storm hardware be attached with stainless steel screws.
- New storms must be primed on all sides and finish-painted before installation.
- Storms must be painted in gloss or semi-gloss paint the same colour as the exterior face of the sash underneath.
- No modifications, cutting, or alterations to the building’s character-defining elements are permitted during storm window installation.
- It is recommended for safety reasons for the storm windows to be openable from the interior.
Download or pring Windows, Doors & Storm Window Requirements
Fascias, Gutters & Downspouts
- Gutter replacement should be coordinated with re-roofing, and both should precede painting.
- Fascia boards and rafter tails should be checked for rot, and repairs included in quotes.
- Do not allow contractors to cut off the exposed or notched rafter tails (typically found on Craftsman houses) to allow installation of larger gutters.
- Do not allow contractors to cut into the water table when attaching downspouts.
- Built-in gutters should be repaired and retained rather than attaching new ones.
- When repairing or replacing deteriorated woodwork, use the same wood species (likely fir or cedar) as the original and ensure that the exact profile of the original material is replicated. (Most modern stock lumber has rounded edges and is likely smaller than the original and may not be an acceptable replacement).
- All new woodwork must be primed with alkyd (oil) primer on all sides at the time of installation.
- Original gutter and downspout materials are preferred (i.e. wood, galvanized metal), but pre-finished enameled steel or aluminum is acceptable if compatible with colour scheme of house.
- Original profile of gutters (typically ogee or K-style) and downspouts should be replicated.
- Downspouts in Victoria were typically round (3″ is available locally). Square downspouts will not be funded unless there is documentary evidence that they were original to the house.
Stucco
VHF funds repairs to historic stucco. VHF also funds removal of stucco, asphalt, asbestos, aluminum or vinyl siding where original siding has been covered by these materials.
- Ensure that any textured or decorative stucco is accurately recorded before undertaking repairs (i.e. note texture, thickness and colour).
- Strength, composition, colour and texture of historic stucco should be carefully matched.
- Consider repairing the entire wall panel or section, but generally do not remove sound stucco.
Roofs
When obtaining estimates for roofing, it is important to provide roofers with a copy of these VHF requirements and ensure that they specify the applicable requirements in their written quotes.
General Guidelines
- VHF funds repairs to roofing including flashing.
- VHF is able to fund re-roofing of a house once every 25 years
- VHF will fund re-roofing with historic material as well as compatible substitutes.
- Substitute roofing material should reflect the historic material in design, colour, exposure, size and other visual qualities. A sample of proposed material, if new to VHF, must be submitted for review and approval.
- Original wooden shingle roofs on historic houses were most commonly stained in shades of red, green, brown, or black. To reflect this traditional appearance, VHF recommends asphalt shingles in black, dark green, deep red, or brown. Grey shingles are not historically appropriate and are therefore not recommended. The selected shingle colour must complement the historic paint colours of the house and maintain the overall heritage character of the property.
- Roofing and gutter replacement should be coordinated (see Fascia, Gutter & Downspout requirements).
- Masonry chimneys require repointing; this should be done prior to re-roofing (see Chimneys & Masonry requirements).
- Ensure that nail length for roof overhang on exposed eaves is correct to avoid protruding nails.
- All new elements (including vents) should be fitted as discreetly as possible.
- Vents must be installed to BC Building Code requirements. Contractor should indicate the number of required vents and discuss placement of the vents.
- Ensure chemical and physical compatibility between roofing material, fastenings and flashings (i.e. do not use copper with galvanized material).
- Low-pitched roofs have specific requirements: refer to BC Building Code or specialist.
- Original ridge capping may have been metal or wood and should be reinstated, if known.
If there is documentation of original rooftop decoration or missing features such as cresting or finials, consider replacing at time of re-roofing (see Special Grants in Application Requirements document).
Woodwork & Trim
- It is always preferable to repair original material where feasible.
- Where the design of missing woodwork elements is unknown, documentary evidence must be provided from buildings of a similar style and era to demonstrate that replicated elements will be appropriate. To ensure historical accuracy, it is recommended that homeowners consult widely with those knowledgeable in the field before undertaking the replacement of missing elements (e.g. heritage architects, designers or engineers, City of Victoria Heritage Planners, VHF House Grants Inspectors). Such preparatory consultations can assist the homeowner in avoiding inaccurate design choices as well as the use of inappropriate materials.
- When repairing or replacing deteriorated woodwork, use like materials (wood species) and ensure that the exact profile of the original material is replicated. (Most modern stock lumber has rounded edges and is likely thinner than the original and may not be an acceptable replacement.)
- Rotted or structurally deteriorated woodwork must be repaired or replaced prior to applying paint.
- All new woodwork must be primed with alkyd (oil) primer on all sides at time of installation (including concealed areas such as stair treads, etc).
- Contemporary products suitable for preservation of deteriorated woodwork should be researched for your projects.
- Composite materials (e.g. plywood, OSB, fibre-cement board) should not be used for exterior cladding without prior VHF approval.
- Most original porches in Victoria between 1900-WWII were decked with Douglas fir tongue and groove flooring, with a standard visible floor width of approximately 3 1/2 inches and ran parallel to the slope. They should be replaced with like materials whenever possible..
- Stair treads should be bull-nosed; cove moulding under the treads may be historically correct for your house.
Painting
To qualify for VHF funding, all preparation and painting must be approved by the Master Painters & Decorators Association (MPDA). MPDA provides project specifications and conducts inspections to ensure a high-quality, long-lasting paint job. The cost of the MPDA inspections should be separately itemized in the painter’s quotes.
The MPDA involvement is a contractual agreement between the homeowner and MPDA. VHF will not mediate between homeowners and contractors and encourages direct communication. No grant will be paid until the MPDA inspection fee is paid, the painting company is paid, and all deficiencies identified by MPDA are resolved.
When applying for a VHF grant, ensure painters are familiar with the MPDA Specifications and process when obtaining quotes. Refer to the links below for more information:
MPDA Technical Specifications (revised January 2023)
MPDA Request for Consultation 2024
MPDA – SSI009 – Request for Specification[28047] 11.2
MPDA Strata Request for Inspection – Dec 1 2024
MPDA Submittal Pages for MPDA Specification Paint
Historic Colour Schemes
Changes to colour schemes require approval through a Delegated Heritage Alteration Permit (DHAP) from the City. This is an expedited process and there is no fee. A Historically-appropriate colour scheme approved for funding by VHF must be one of the following:
- Professionally-documented original colours.
- Historically-appropriate colour schemes. Please refer to Your Old House, True Colours and Historical True Colours for Western Canada for more information including correct colour placement. Be sure to understand what style your house is (e.g. Queen Anne, Italianate, Craftsman, etc.) when referring to these sources.
VHF Colour Scheme Requirements
- Submit the following for consideration and approval by VHF:
- Copy of DHAP application submitted to the City if colours changed.
- Sketch or coloured-in photocopy illustrating colours and their placement on the architectural elements of the house.
General Guidlines
The following are general guidelines for painting a historic wood houses:
- Exterior repairs should be completed before exterior painting: i.e. foundation, roofing, drainage, windows, woodwork and trim repairs.
- Woodwork repairs to rotten siding or window sills should be completed before painting.
- Loose or warped siding or shingles must be nailed flush with surface using appropriate nails.
- Loose or deteriorated window putty must be removed and replaced with linseed oil glazing putty. This will need to be done by others, as linseed oil putty requires several weeks drying time before alkyd/oil primer can be applied.
- Doors and trim molding are to be MPI Gloss level 5 or higher.
- Exterior painting should be done when air and surface temperatures remain above 10°C for at least 24 hours before, during and after paint application.
- Wood moisture content should not exceed 15%; use a moisture meter.
- No exterior painting should be done when the relative humidity is above 85% or when the dew point is less than 3°C variance between the air temperature.
- Downspouts and other removable hardware should be removed prior to painting and reinstalled upon completion.
Preparation
The most important aspect of a paint job is preparation of the surface to be painted. An improperly prepared surface will not hold paint. If done correctly the first time, then maintenance will be less frequent and subsequently much easier.
- Proper safety procedures should be observed when removing existing paint or surface coatings.
- Remove damaged or deteriorated paint to the next sound layer using the gentlest method possible (scraping and sanding).
- No media (e.g. sand) blasting.
- No stripping by torch
- Ensure a clean surface, free of grease, dirt, mildew, etc. by washing wall surfaces, overhangs, porch ceilings and eavestroughs, inside and out, by hand with environment-friendly cleaners. Rinse thoroughly.
- Washing is acceptable by hand and garden hose.
- Crystalline deposits, which develop under eaves and protected areas, are a major cause of peeling; remove by washing and rinsing as above.
- Power washing historic wood is not recommended and should never be used as a means of removing paint.
- Power washing may be used to clean the existing paintwork, however, ensure that the operator is experienced with historic wood and that low pressure below 600 psi is used.
- Water spray should always be directed downward and kept away from openings in the siding.
- House must dry between washing and painting to ensure the surface will not resist new paint. Wood moisture content should not exceed 15%; use a moisture meter.
- Areas of heavy paint buildup, alligatoring, blistering, scaling and peeling, or areas which show a moderate to heavy chalk deposit must be thoroughly prepared to ensure paint adhesion. Remove to a sound substrate by scraping, wire brushing and sanding.
- No grinding or heavy abrasive sanding that damages the wood surface.
- Glossy surfaces under eaves and protected areas that are not exposed to normal weathering should be dulled by sanding.
- Where bare wood is exposed, prime with a high quality alkyd (oil) primer.
- Loose or warped siding and shingles must be nailed flush with surface using appropriate nails.
- Fill all crevices, nail holes and cracks.
- All loose or split caulking is to be removed and replaced. Re-caulk with flexible, paintable caulking, and then prime.
- Do not apply paint in direct sunlight.
Painting or Staining Shingle Siding
- Shingle siding should be stained unless already painted
- Stains penetrate the wood surface and are less likely to peel.
- On rough-sawn textured shingles, previously stained weathered surfaces must be thoroughly cleaned with a stiff fibre brush and a mild, biodegradable remover such as sodium hydroxide, to remove “dead” wood fibres.
Paint Types
- A minimum of two coats of top-quality paint should be applied; film thickness as per material specifications.
- Choice of paint will depend on condition of surface, the existing undercoat, location on house and design of house.
- Window sashes, doors, frames and trim must be done in gloss or semi-gloss.
- Doors and trim moldings are to be MPI Gloss level 5 or higher.
- Old stains in wood will leach through latex paint. Wood must be sealed with an alkyd (oil) primer.
- Half-timbering was likely meant to have a flat finish, to simulate an aged, medieval, rough-hewn look.
Lead Paint
- If you are planning to paint the exterior of your house, you should be informed about the dangers of lead paint. Lead was common in exterior paint manufactured before 1990. You should assume that any home built before 1990 contains some lead paint. Lead in paint becomes a hazard when it is breathed in as dust created by sanding, grinding or cutting, or is otherwise ingested as chips, flakes or from residue rubbing off onto food through dusty/contaminated hands. You, your children, your neighbours and the workers can be exposed to lead any time you breathe lead dust, fumes, or swallow anything that contains lead. While lead in paint can be a serious danger, it can be safely removed.
- Worksafe BC requires proper testing and procedures for handling and the disposal of lead paint. VHF will reimburse homeowners applying for a painting grant for lead testing by a qualified hazardous material testing company up to a cost of $250. This should be completed prior to obtaining quotes for painting. Please contact VHF for more info.
Application Form

642 Battery Street
ARCHITECTURE: This architect-designed, 1½-storey, hip-roofed, Queen Anne cottage has two identical, hip-roofed angled bays on the front. All the hips on the house have finials. The house type, including Italianate examples, became popular in Victoria around 1890 (340...
1109 Catherine Street
ARCHITECTURE: Rose Cottage is a vernacular Queen Anne house. In 1905 the Siebenbaums doubled the width of their main rooms by adding a second bay on the main floor and an upper balcony on top of the now double bay. The upper balcony consists of round columns...
1458 Begbie Street
ARCHITECTURE: This is one of Victoria’s most unusual Queen Anne houses because of its dramatic roofline. The roofline consists of two steeply cutaway gables which are perpendicular to each other. Under these are two offset gables, the lower of which covers the front...
2744 Avebury Avenue
ARCHITECTURE: This 1½-storey, side-gabled Craftsman house is rare for Victoria because it is built mostly of stone. The roof is bracketed and has exposed rafter tails; it is dominated by a large shed-roofed sleeping porch with a Tudor arch. There is a full-width,...